By Greg Whitaker www.constructionweekonline.com
Getting the first two lines of Dubai’s new metro system raised from sand to full operation in just five years is the sort of task that Brunel himself might have baulked at. Add the fact that the project has to run through built up areas and through existing road networks, you might be able to understand the difficulty of the operation.
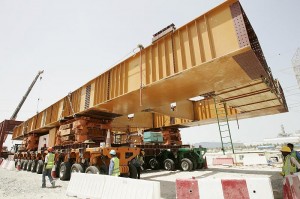
At first, Dubai’s Road and Transport Authority (RTA) searched for an engineering firm with the experience and size to deliver something of the type. Eventually they awarded an AED 12.45 billion contract to a consortium of Japanese companies including, Mitsubishi Corporation, Obayashi Corporation, Mitsubishi Heavy Industries, Kajima Corporation and Turkish firm Yapi Merkezi.
Work began in 2005, with scores of subcontractors brought in. Amazingly there was no in-house plant department at first, but very soon it was obvious that one was needed so the ‘department that never was’ got established and underway.
Headed by Graham Larkin, the new division comprised of lots of machines, and even more hardware to keep them running as well as scores of people to make it all work.
Anywhere with a lot of kit and people needs to be well organised, so the plant manager employed a modern approach to efficiency. “We use the Tag Plant Management System. It was originally developed for the oil industry,” explained Larkin. “I should have been a salesman for it, I’ve used it in my last three or four projects,” he smiled.
The computer helped log all the pieces of kit that were being bought in, along with their serial number, current location and service record.
In theory, the operation was paperless, but in practice there were reams flying everywhere, as safety certificates, manuals, transfer documents and the like came in. With the system up and running, a keen team of staff started logging all the machines, from their demountable office at the Deira City Centre site.
“We have a responsibility to make sure all the paperwork from our equipment and the subcontractors equipment is all in order.” Larkin said.
Keeping track of all the machines on a jobsite that snakes around 166 km is no walk in the park though. “It’s a difficult job, because it all comes in one day and then is out somewhere else again on another.
”We make an arrangement to go to the site to inspect whatever the machine is. All the mandatory documents are in place and if they are not, they are not to use it. So we have quite a mountain of files,” he laughed.
The number of machines that were being entered into the system became mind boggling. “I wouldn’t even hesitate to guess the amount of subcontractors machines there are on the job at the moment – literally thousands,” explained Larkin. “Our own equipment list comprises of 423 items from lighting towers upwards.”
A particularly arduous job is keeping on top of the paper work for the piling rigs, of which various contractors have a couple of dozen around the site.
By their nature, they are constantly being moved, but every time one leaves the gets moved out onto the road, so that it can be used elsewhere on site, the law states it has to be inspected again, meaning the paperwork starts ‘piling’ up for the plant department.
Interestingly, the giant two-metre diameter double-start drilling buckets used in the pilers had to be custom made by a local firm in Dubai, as such a thing is not an off-the-shelf item, even in Mitsubishi Heavy Industry’s long inventory.
Speaking of the inventory, one of the largest areas in the plant department is a fleet of 61 trucks. Several of these are Mitsubishi Canters, which have had various custom backs installed, notably that of a crane inspection platform and mobile tire rig. All have had flashing strobe lights fitted to the rear as well as high-visibility chevrons, as the narrow job sites that work through the night mean all precautions need to be taken in order to prevent site vehicles bashing bumpers.
Other trucks owned by the depot include one 50-tonne tractor unit, which has the sole purpose of shifting rebar, while another moves aggregates. These, alongside an assortment of cement mixers and dumpers are only seen during the hours of darkness due to the rules affecting the movement of heavy vehicles on the Emirate’s busy roads throughout the day.
”This is another, operational reason why the site has to run 24 hours,” explained Larkin.
Also running right through the night is a forest of mobile cranes. Complementing the countless scores of contractor’s units throughout the jobsite, are 24 rough terrain cranes belonging to the plant department.
Smaller site managers might take comfort in the fact that the region’s chronic equipment shortages in recent years even affected well-resourced projects like the metro. There were simply no new cranes to be had, so the plant manager had to look further a field. “We got them from all over Europe,” said Larkin.
“We basically concentrated on three types and that was really dictated by what was on the market at the time.”
The new cranes all dated from the twenty-first century, as the plan was to update the fleet as much as was possible, as most of the existing stock was quite old, with many thousands of hours on the clock.
The updated fleet included a Liebherr 35-tonne unit from 2002, a pair of ex-Japan Grove cranes and a Terex-Demag AC 40 city crane, which at the time of our visit was having the previous owner’s decals removed from the boom, in preparation for a fresh coat of paint.
“We have quite a good show of newish cranes, and they are all quite well equipped in the safety department.” Larkin said. “They have proper, up-to-date safe indicator systems, made by Kruger and Liebherr-Likon. These are fail-safe, so even if the computer packs up, it’s still a crane.”
The newer cranes supported about forty older mobile units, the most elderly of which were a pair of 20 year old 50-tonne units, made by Grove and Tadano respectively.
There are also a few rental units, including a mighty 450-tonne Demag, which worked with the tunnel boring machine (TBM) deep underground. A fleet of mini Kobelcos also helped underground.
Back on the surface, there are more useful things happening in the City Centre site. Welding kits buzz, as workers fabricate lighting towers by the dozen. There are machines to paint, certificates to file, deals to do. And this is how it will remain, day and night, long after the job is complete.