By Hugh Naylor www.thenational.ae
Dubai // When Dubai’s Metro opens on Wednesday as one of the largest public transport systems in the Middle East, officials will be expecting, among its benefits, that it will be an artery to unclog roads congested by years of rapid development.
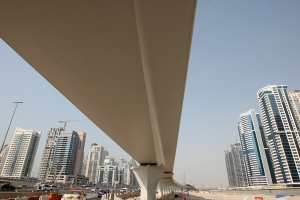
Among the primary reasons for building the Metro, according to the website of the Roads and Transport Authority (RTA), which heads the project, are to provide an alternative mode of transport to ease congestion, save passengers travelling time and reduce traffic pollution.
An essential component of this endeavour is the viaduct system – elevated tracks on which passengers in automated, driverless trains will pass smoothly above thoroughfares and businesses.
Although it is now fast becoming a memory, the assembly of the line, which began in March 2006, was a test of brains and brawn.
Japanese consortiums and multinational architectural firms had to figure out how to rapidly link together, in a dense, urban environment, what would ultimately be 11,400 segments of concrete track bed for the Red Line alone.
The sections, weighing nearly 50 tons each, had to be transported along busy roadways, hoisted off the ground by mammoth cranes and locked into place.
But first, engineers had to find a location that was large enough – and relatively close to the building project – for the thousands of segments of track deck to be cast.
The solution was a massive facility in Jebel Ali. At peak production, the complex churned out nearly 47 sections of track deck a day – nearly 800 cubic metres of concrete. To aid in the delivery of the deck sections were 10 on-site gantry cranes, each capable of hoisting 90 tons.
At night, when they did much of their work, floodlights illuminated the mammoth machines as they gently positioned slabs of concrete and steel as an estimated 800 labourers directed their movements with hand signals and high-pitched shouts.
In an undertaking involving weights in the hundreds of tonnes, getting the fine details right was also crucial.
Minute planning could mean the difference between success and disaster, and it required gauging Dubai’s soil composition and reinforcing the concrete against movement that, even if slight, could result in catastrophe.
The 1,450 piles that support the Red Line’s viaduct had to be given additional protection against “aggressive ground conditions”, according to a 2008 article in Concrete Engineering International, an industry magazine.
“Durability considerations were paramount,” the article said, requiring additional waterproofing to improve resistance to chloride attack and other reinforcements to improve resistance to sulphate attack.
The structure was given additional strength through the mixing of several types of cement, including ground granulated blast furnace slag, which significantly extends the life span of concrete structures and is increasingly being used in durable concrete around the world.
What it was like for an individual worker on such a mammoth project can only be left to the imagination. Officials at the RTA declined multiple requests for interviews, and companies involved in the project declined to comment, telling journalists that they first had to receive approval from the RTA.
But workers must have experienced tedium as well as anxiety, such as when a massive crane working on the Trade Centre Station collapsed on Sheikh Zayed Road in November.
The collapse caused kilometres-long traffic jams, and nearby vehicles would have been crushed were it not for a gantry road sign that broke the crane’s fall.
But now, glitches aside, it must be a gratifying experience for those involved in the project, because what is one of the world’s most advanced public transport systems may also breathe new life into all of Dubai.